Stop the Loss with Safety First | GLOVETEX.COM
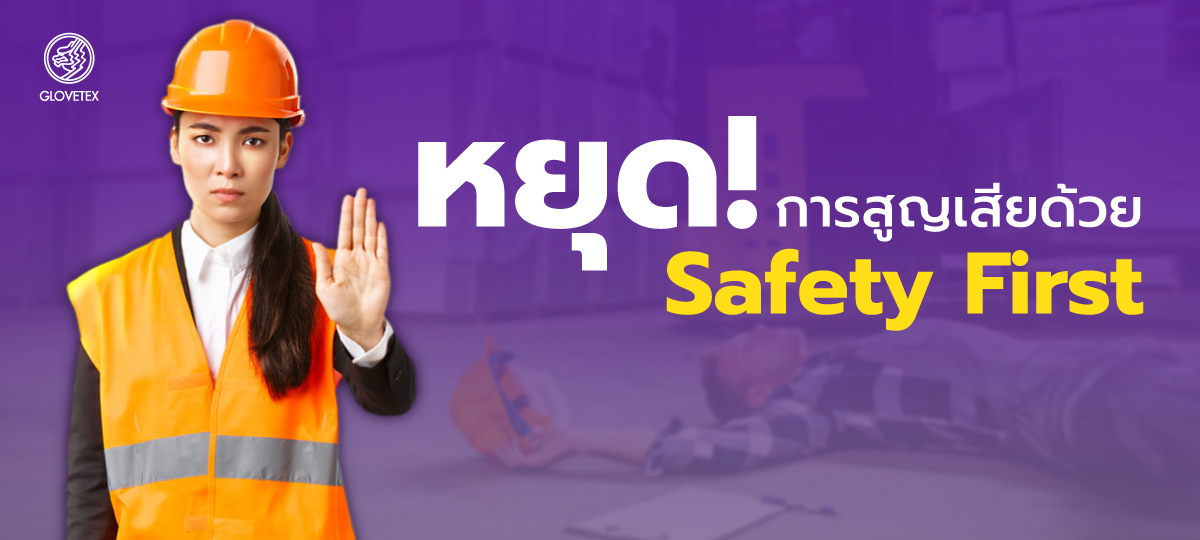
Workplace safety is a critical issue that should never be overlooked. Each year, many lives are lost due to accidents and incidents in the workplace. It is crucial for employers and employees to prioritize safety measures and take proactive steps to prevent fatalities. One of the most effective ways to ensure workplace safety is through the use of Personal Protective Equipment (PPE). PPE acts as a shield against potential hazards, significantly reducing the chances of injuries and fatalities. From helmets and safety goggles to gloves and earplugs, various types of PPE are designed to protect workers from specific risks. Enforcing the use of PPE and providing proper training on its use can greatly reduce the number of work-related fatalities. Remember, prevention is always better than cure, and investing in PPE is an investment in the lives and well-being of your employees. Together, we can stop workplace fatalities and create a safer working environment for everyone.
Everyone, at all levels within the organization, has a role to play in promoting safety. It begins with each individual prioritizing safety first—what we call “Safety First”—and fully engaging in every aspect of safety-related work to help prevent accidents and losses before they occur. Here are 10 key areas to focus on:
Safety and Occupational Health Policy
Establish a safety policy in line with ISO 45001: 2018, where top management must create, implement, and maintain the policy with commitments such as:- Providing a safe and healthy work environment to prevent injuries and illnesses, suitable for the organization’s purpose, size, and context.
- Setting a framework for safety objectives.
- Complying with legal requirements.
- Eliminating hazards and reducing safety risks.
- Continually improving safety performance.
Training and Education
Provide training based on legal requirements, specific job risks, and other organizational needs. Key stakeholders: management, all employees, contractors, and subcontractors.Safety Inspection Planning
Conduct regular inspections using the PDCA (Plan-Do-Check-Action) cycle, and address any deficiencies found during inspections. Key stakeholders: safety inspectors.Job Safety Analysis and Standard Operating Procedures (SOPs)
Identify hazards, assess risks, prioritize, and control risks by establishing SOPs for safe work practices. Key stakeholders: supervisors, technical officers, and safety professionals.Work Observation
Monitor adherence to SOPs, identify, and eliminate risky behaviors. Key stakeholders: safety committees, supervisors, and safety professionals.Worker Health Control
Analyze work environments, monitor health, and control risks. Key stakeholders: safety professionals, health services, and HR.Hazard and Risk Control
Implement controls in the following order:- Elimination
- Substitution
- Engineering controls
- Administrative controls
- PPE usage
Key stakeholders: safety professionals, engineering teams, and workers reporting unsafe conditions.
Communication
Ensure internal and external communication on safety policies, guidelines, and procedures through appropriate channels. Key stakeholders: communication teams.Procurement Control
Implement safe procurement processes considering worker health and safety. Key stakeholders: procurement teams.Promoting Safety On and Off the Job
Engage in activities that promote safety consciousness both at work and in personal life, such as at home, on the road, or during leisure. Key stakeholders: everyone in the organization.
information. or request a quotation
Call Center: 034-878762 ext. 3
Or you can follow us at : Click here
Hotline 083 989 7512 (telephone sales department)